How 3D Printing Technology is Revolutionizing Building Construction
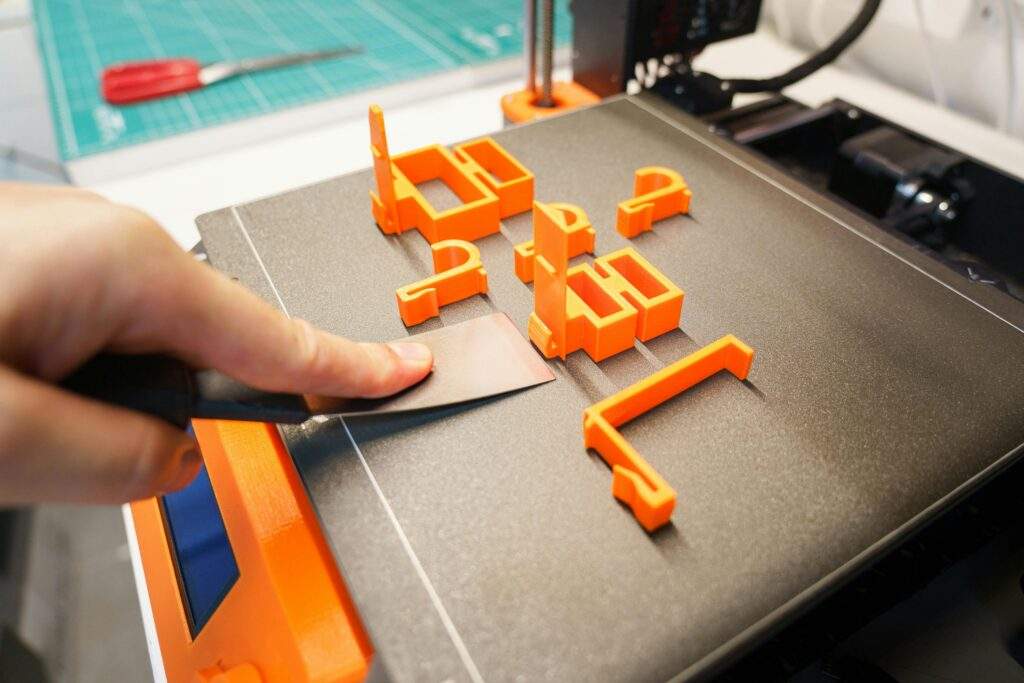
3D printing, also known as additive manufacturing, is making waves in the construction industry, transforming how buildings are designed and constructed. This cutting-edge technology offers immense potential to build complex structures faster, more sustainably, and at a lower cost. In this blog post, we will explore how 3D printing technology is used to construct buildings and its impact on the construction industry.
1.What is 3D Printing technology in Construction?
3D printing in construction involves the use of large-scale 3D printers to fabricate building components layer by layer using materials like concrete, polymers, or recycled substances. Instead of traditional methods that require manual labor and a long timeline, 3D printers follow a digital model to create structures quickly and precisely.
2.How Does It Work?
The process of constructing a building using 3D printing starts with a digital blueprint, usually designed with Computer-Aided Design (CAD) software. This digital model is fed into the 3D printer, which uses a robotic arm or nozzle to lay down layers of the building material. Each layer is added precisely based on the digital plan, allowing for rapid construction of walls, foundations, and even entire structures.
3.Key Materials Used
Concrete: The most common material in 3D printed construction is concrete. Special types of concrete mixtures are used that can be extruded smoothly and set quickly.
Polymer Composites: Some projects use polymer-based materials for flexibility and insulation.
Sustainable Materials: Recycled materials or eco-friendly composites are becoming increasingly popular in 3D printing, reducing environmental impact.
4.Benefits of 3D Printing technology for Buildings
Faster Construction: Traditional building methods can take months or years, whereas 3D printing can significantly reduce construction time. A small house can be printed in just a few days, speeding up housing projects.
Cost-Effective: Since 3D printing uses precise amounts of material with minimal waste, the cost of raw materials is reduced. Labor costs are also lower as fewer workers are needed to operate the machinery.
Design Flexibility: Architects can experiment with complex designs and shapes that would be difficult or expensive to achieve using conventional methods. 3D printing opens up creative possibilities that were previously limited by construction techniques.
Reduced Waste: Traditional construction methods produce more material waste. 3D printing uses only the necessary material for each layer, leading to less waste and a more sustainable construction process.
Durability and Precision: The controlled, layer-by-layer printing process provide stable structure, which can improve the overall strength and durability of the structure.
5. Applications in Real-World Projects
3D printed homes are already being tested as a solution to housing shortages. In countries like Mexico and the US, entire communities of 3D printed homes have been developed for low-income families.
Emergency Shelters: In disaster-stricken areas, 3D printing offers a quick way to construct temporary or permanent shelters for displaced populations.
Commercial Buildings: Large-scale construction projects, such as offices or public buildings, are also adopting 3D printing for faster, more efficient project completion.
6. Challenges and Limitations
Initial Investment: Although 3D printing saves on long-term costs, the initial investment in the equipment and technology can be high for smaller construction firms.
Regulatory Hurdles: Since 3D printing in construction is still relatively new, building codes and regulations have yet to fully catch up, which can cause delays in project approval.
Material Constraints: While 3D printing is versatile, it is currently limited by the types of materials that can be printed efficiently. Concrete works well, but metals and other materials pose challenges for large-scale use.
7. The Future of 3D Printed Buildings
The future of 3D printed construction looks promising, with advancements in material science and automation. As technology evolves, we can expect buildings to be constructed faster, more affordably, and with more creative freedom. Eventually, entire cities could be built using 3D printing technology, reducing both construction time and environmental impact.
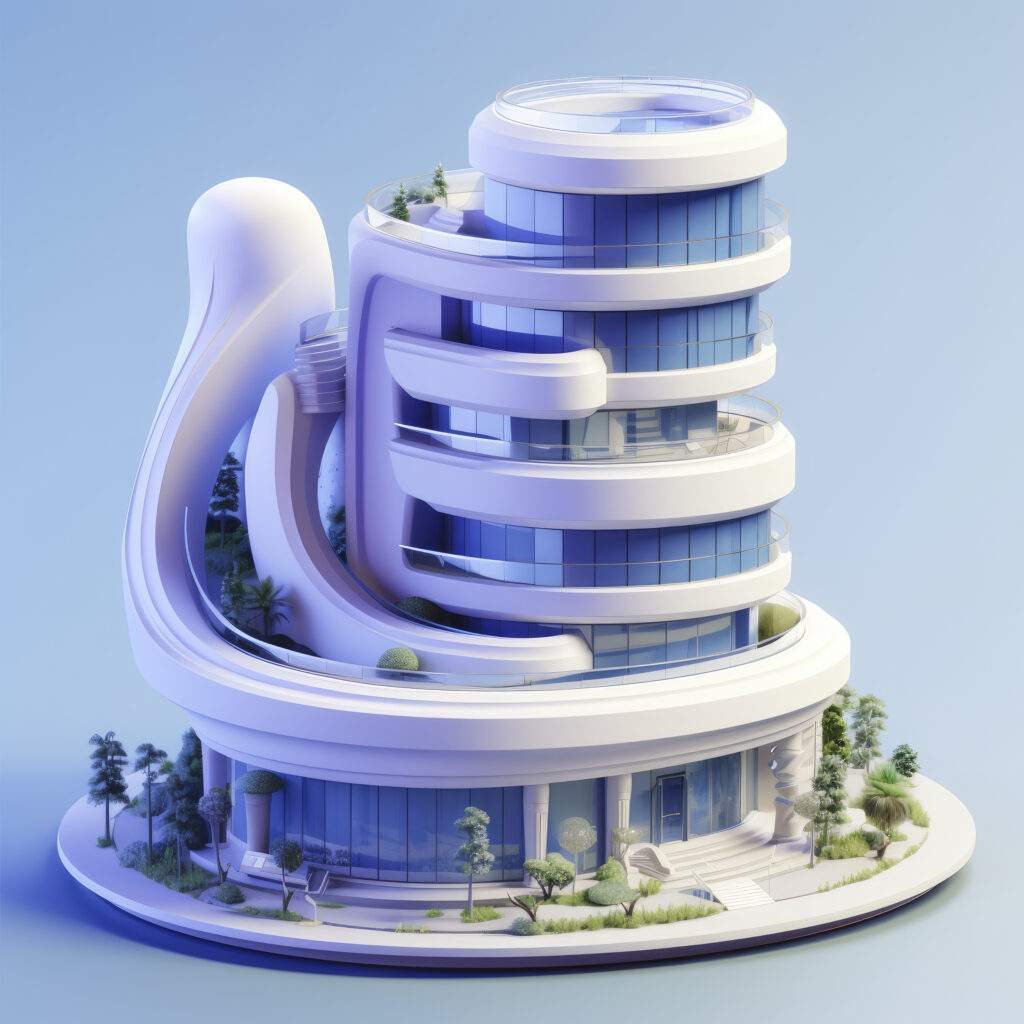
8.Cost used for 3D Printing Construction
The cost of building a 3D-printed home can vary depending on factors such as location, size, materials, and the complexity of the design. However, 3D-printed homes tend to be much cheaper than traditionally built homes due to lower labour and material costs. Here’s a general breakdown of what you can expect:
8.1. Estimated Costs for a 3D-Printed Home:
Small Home (300-400 sq. ft.) Cost: $5,000 – $10,000
Medium-Sized Home (600-800 sq. ft.) Cost: $10,000 – $30,000
Affordable housing projects for small families often fall into this category. Some organizations aim to print homes in this size range for developing nations.
Larger Home (1,000-2,000 sq. ft.) Cost: $30,000 – $100,000
Example: These homes can be built as permanent residences with multiple rooms, including living spaces, kitchens, and bathrooms.
8.2. Factors Affecting 3D Home Costs:
Material Costs
Most 3D-printed homes use concrete, which is relatively affordable. However, if other materials like polymers or sustainable materials are used, the cost could increase.
Labour
Since the process is largely automated, **labor costs are lower**. Fewer workers are needed, which reduces overall expenses, especially for larger homes.
3d Technology and Equipment
The initial investment in 3D printing equipment can be high, but once in place, it reduces per-home costs significantly. Companies with large-scale 3D printers can offer competitive pricing.
Location
Costs can also vary by geography. For example, rural areas may have lower regulatory costs, while urban areas might have stricter building codes and higher land prices.
Complexity of Design:
More intricate designs, unique shapes, or specialized features (e.g., custom roofs, windows) can drive up the price.
8.3. Cost Comparisons with Traditional Homes:
A traditionally built home in the U.S. typically costs $100,000 – $200,000 or more for a similar size and quality. In contrast, 3D-printed homes can reduce these costs by 30-60%
Examples:
ICON, a U.S.-based 3D printing construction company, has created homes for as little as **$10,000**. In Mexico, a nonprofit organization printed a small community of homes for about **$4,000 – $6,000 per house**.
As technology advances and becomes more accessible, it’s likely that 3D-printed homes will become even more affordable, providing a viable solution for housing shortages and sustainable construction.
3D printing technology is revolutionizing the construction industry, offering a blend of speed, efficiency, and sustainability. With its potential to build affordable, durable, and eco-friendly structures, it is poised to address some of the world’s most pressing challenges, such as housing shortages and sustainable development. As more companies and governments adopt this technology, 3D printed buildings could soon become the new normal in construction.
This is just the beginning of a technological shift that could redefine how we build and live in the cities of the future.